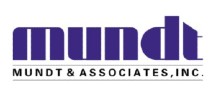
Mundt meets new technology demands for Micromachining & Miniaturization with the
new MUNDT AB-200150-5 Laser Workstation in addition to other standard machines
with micromachining capabilities.
This new Workstation, the AB-200150-5, is built with Granite and Ceramic to achieves
EXTREME accuracies that permit machining of tiny detailed features. Complex beam
delivery provides an extremely small spot with a Galvo. Infinite Field of View allows
accurate and seamless machining, with the Galvo and cartesian axes, that the scanner
optics alone, cannot provide
Reasons to Embrace Laser Micro Machining Technology
Todays advanced designs demand Extreme Accuracies, High Throughput, Competitive Pricing and Solid Technical Support.
Industry now requires components with smaller features that require new processing with dependable high accuracy technology. It is now possible to choose the best materials for the job eg. Silicon, Platinum, Glass, Animal Tissue, Kevlar, Stainless Steel, Plastics, Copper, Gold etc. that are difficult or impossible to machine with other methods.
Save money and get substantial ROI with high yields, more efficiency, greater productivity – your machine will pay for itself quickly and Mundt will upgrade and
service your machine for as long as you have it.
See Standard machine suitable for micromachining at www.mundtinc.com.
![]() |
![]() |
|
The Micromachining & Miniaturization Platform Mundt & Associates Inc. was an early pioneer of utilizing laser technology for manufacturing and has successfully developed a wide array of standard and custom laser workstations. Laser machines can be utilized for research and development, or dedicated production machines. They are robust laser workhorses capable of operating 24/7.For many years Mundt has been focusing on micromachining for those companies that are required to build miniaturized products. Mundt offers proven Standard machines that designed and developed to manufacture minute parts and fine components with micron scale features. |
Ultra-Fine Micromachining Mundt & Associates has been working with clients to provide solutions for manufacturing minutely detailed products for many years. Now industry is demanding even more miniaturization. Laser Micromachining can be defined as a process used to produce fine features in tiny parts that are measured in microns. Precision machines combined with the latest laser technology, ultra-short pulse or fiber laser technologies are used to achieve precise cutting, drilling, welding and ablation features. |
Infinite Field of View (IFOV) Efficient high precision laser micro machining requires a galvo scan head with a short focal length and seamless coordination with motion stages. This technique is called Infinite Field View (IFOV). Part sizes are only limited by stage travel size. Fine details are managed by the galvo scan head and larger features are handled by the galvo and stages in seamless motion. |
![]() |
![]() |
![]() |
Air Bearing Stages Air Bearing Stages would be selected for micromachining tiny parts with ultra-fine features. Air Bearing Stages enable high precision, as the stage “glides” on a cushion of air that allows smooth, controlled motion for PRECISE operations. Air Bearing Stage systems can deliver sub-micron accuracies. The Mundt Air Bearing Stage when paired with Ultra Short Pulse Lasers provide the ultimate micromachining workstation. |
Laser Micro Welding Laser micro welding utilizes the high speed and accuracy of Mundt systems to join two materials with precisely controlled weld penetration. As the industrial market needs grow and become more complex, laser-processing techniques must expand. Mundt has the technology to provide sub-micron accuracies for the production of a prototype through high production runs. The company has the capability to process products from simple two-dimensional parts through to the most complex shaped parts using multi-axis machining. |
Laser Ablation Selective laser ablation is applied where material needs to be removed without damage to surrounding areas.Ablation processes are needed for applications that require a minimal heat effective zone. This process is accomplished with the use of computer controlled ultra-short pulse lasers that provide precision depth control of fine details. The ablation process produces a clean feature that is delivered without heat damage. |
![]() |
![]() |
|
Laser Micro Drilling Laser micro drilling is required to drill tiny holes, in the micron range, that are used in the electronics and other industries. Tiny features, small holes, slots or patterns are required for many complex processes. The precise drilling of very small diameter holes requires an array of details and components that are critically significant. Laser micro drilling requires a solid robust machine tool paired with the appropriate laser for the application. Mundt offers several standard machines to fit these demanding requirements, all backed by outstanding support. |
Laser Micro Cutting Precision Laser Cutting is a micromachining technique suitable for a variety of materials. Laser micro cutting can achieve features down to submicron sizes. Lasers create narrow kerfs for fine details and minimize material loss when expensive materials are used. Computer controlled Micro laser cutting machines allow for fast configuration changes and are applicable to development through large-scale production. The benefits of laser cutting are small kerf widths, with minimal heat input for critical applications. |
Fig.1
Scanning Electron Microscope (SEM) image at 5000 X magnification of a laser bond with about 800nm of weld penetration into the bond pad. The Laser Ribbon Bond (LRB) cross section shows precise penetration control.
Fig. 2
This is a laser bond magnified 300 X
Fig. 3
Shows the side-by-side results of fatigue tests done on the ultrasonic wire bonds vs. laser bonds. The results shown of this test demonstrates the fatigue life of the laser bond that Interconnects, is several orders of magnitude better than comparable ultrasonic aluminum wire bonds.