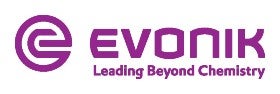
In so doing, the specialty chemicals company is setting new standards for developing and manufacturing custom-made plastic implants, which can now be created using additive manufacturing processes that meet the requirements of ASTM F2026 (the standard specification for PEEK polymers for surgical implant applications).
Sold under the brand name VESTAKEEP® i4 3DF, this PEEK filament is an implant-grade material based on VESTAKEEP® i4 G, a highly viscous, high-performance polymer from Evonik. Customers will be impressed by the product’s biocompatibility, biostability, x-ray transparency, and easy handling. The filament is produced under cleanroom conditions and then subjected to stringent quality management standards for medical materials.
PEEK FILAMENT FOR FUSED FILAMENT FABRICATION
The high-performance material was developed for fused filament fabrication (FFF) technology. The natural-colored PEEK filament, which has a diameter of 1.75 mm, is wound on 250- or 500-gram spools suitable for direct use in standard FFF 3D printers for PEEK materials.
“For modern medical technology, the development of our first 3D-printable implant material opens up new opportunities for customizing patient treatments. Orthopedics and maxillofacial surgery are examples of areas where this could be applied,” says Marc Knebel, who heads the Medical Devices & Systems market segment at Evonik. “Innovative high-performance materials like Evonik’s VESTAKEEP® PEEK—along with highly complex hardware and software, and the perfect match between materials and machines—form the basis for a sustainable 3D-printing revolution in medical technology. Therefore, we will successively expand our product portfolio of 3D printable biomaterials.”
TESTING GRADE ENABLES COST-EFFECTIVE PROCESS ADAPTATION
In addition to its implant grade, Evonik is also offering a testing-grade version of its PEEK filament. The term refers to a class of material having the exact same product properties as the implant grade, but without the documentation needed for approval in medical technology applications. This offers a cost-effective way of adapting the processing characteristics of the high-performance plastic to a given 3D printer.
For more than 20 years, Evonik has been the world’s leading manufacturer of high-performance polymers and additives used in additive manufacturing. The specialty chemicals company offers the industry’s most extensive portfolio of GMP-grade biomaterials used in the 3D printing of medical device parts designed for temporary and permanent body contact. In addition to VESTAKEEP® i4 3DF, the portfolio includes the RESOMER® line of bioresorbable filaments, powders and granules for implantable medical devices.
FURTHER INFORMATION
Evonik’s biomaterials for 3D printing
COMPANY INFORMATION
Evonik is one of the world leaders in specialty chemicals. The company is active in more than 100 countries around the world and generated sales of €13.1 billion and an operating profit (adjusted EBITDA) of €2.15 billion in 2019. Evonik goes far beyond chemistry to create innovative, profitable and sustainable solutions for customers. More than 32,000 employees work together for a common purpose: We want to improve life, day by day.
ABOUT RESOURCE EFFICIENCY
The Resource Efficiency segment is led by Evonik Resource Efficiency GmbH and produces high performance materials and specialty additives for environmentally friendly as well as energy-efficient systems to the automotive, paints & coatings, adhesives, construction, and many other industries. This segment employed about 10,000 employees, and generated sales of around €5.7 billion in 2019 from continuing operations.