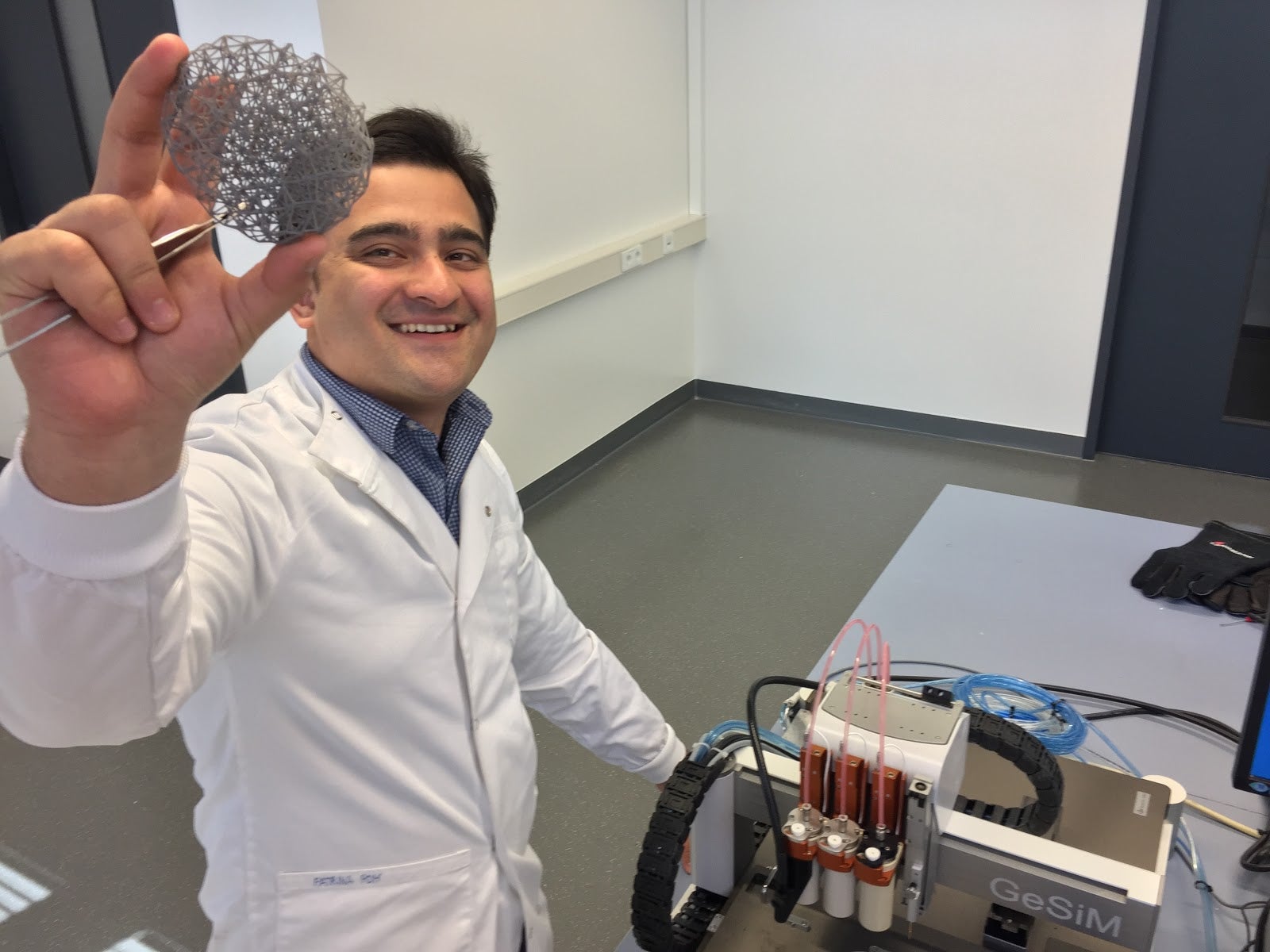
BellaSeno, a company that develops absorbable breast implants using 3D printing, today announced it has obtained full ISO 13485 certification – the international QMS standard for medical devices – for its design and additive manufacturing processes.
The German biotech start-up, founded in 2015, also raised a further $1.1m from existing investors, bringing its total fundraising to $4.73m.
This will be used to fund a clinical trial for its first product, a biocompatible and fully absorbable breast scaffold.
Dr Simon Champ, CEO at BellaSeno, said: “We are now one of the very few companies worldwide with an ISO 13485 certification covering the entire process of design and additive manufacturing of absorbable implants.
“This is not only a prerequisite for the clinical trial of Senella, our first product, but also for closing contract manufacturing deals with companies seeking to develop and market their own absorbable implants for a wide range of medical applications.
“We are offering the entire process under ISO 13485 certification to other medtech companies worldwide – from concept and inhouse design to the manufacturing of prototypes, clinical trials and series production.”
He added that BellaSeno’s platform technology and patent-pending porous architectures can be used to design and manufacture a broad spectrum of soft and stiff devices for bone and soft tissue replacements.
How are the breast implants developed by BellaSeno more natural and safer?
BellaSeno believes it has the potential to disrupt the current breast surgery market, which at present is dominated by silicone implants that are prone to rupture and can require replacement.
Based in Leipzig, Germany, the company’s aim is to create safer and more natural implants that support the growth of breast tissue and are safely absorbed into the body.
It uses polycaprolactone, a biocompatible and bioresorbable polymer that is already used in FDA-approved and CE-marked products for other medical procedures.
Both animal and human clinical trials are scheduled for later this year.
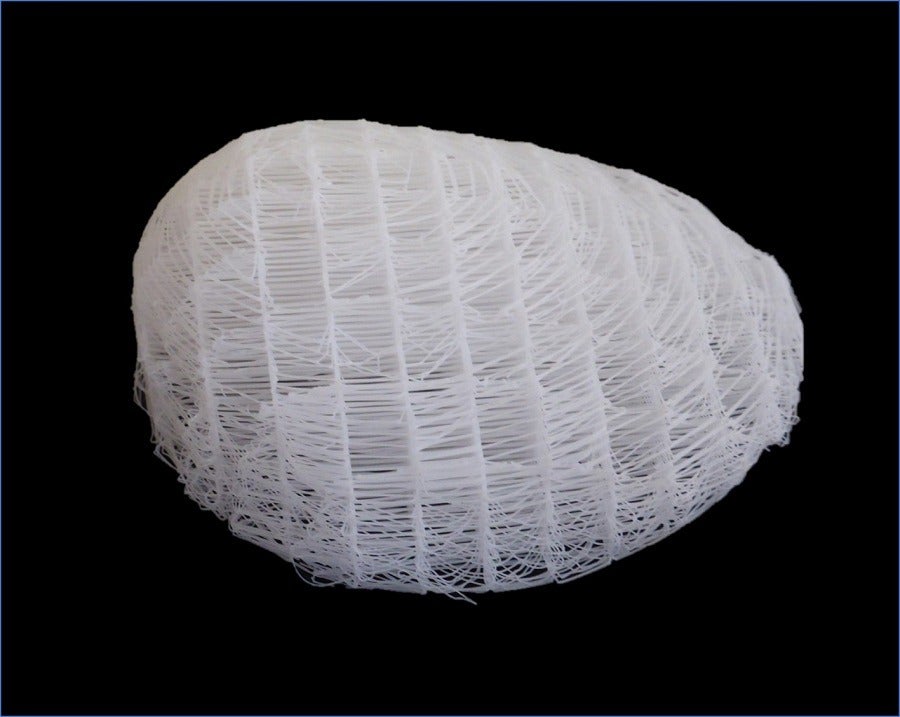
The 3D-printed implants would be available for breast reconstruction after a mastectomy or for elective plastic surgery for breast enhancement.
During the process, the implant guides the growth of natural tissue from lipoaspirate, which is derived from the patient’s own body via a routine liposuction procedure.
Developed using 3D printing, multiple preclinical studies have shown that the implants are slowly absorbed by the body, and the result is a natural tissue with no foreign body remnants.