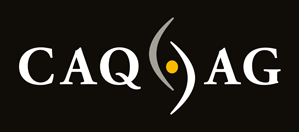
Wild & Kupfer was founded in Switzerland in 1979, and currently has over 170 employees who produce high-tech plastic parts with the help of 85 injectionmoulding machines. All areas of Wild & Kupfer work strictly in accordance with ISO 9001 and ISO 13485. Hence, quality management is subject to the highest demands. As the existing QM-software was getting on in years and neither support nor further development was possible, the company set out in 2015 to find a new quality management software supplier. Wild & Kupfer first drew up a detailed specification sheet against which a large number of potential applicants had to measure themselves.
Committed to quality
The specification sheet contained both basic technical requirements for the software solution to be used as well as detailed requirements, which were oriented to the respective areas of application. The software solution would need to be modular, validatable and connectable to the ARBURG “ALS” host computer system. In addition, it had to meet the ISO 9001, ISO 13485 and ISO 14001 standards, and, in particular, the FDA requirements regarding authorisation concept, audit trail and corresponding approval processes.
The prospective manufacturer of the software solution also had to be an established provider, with a verifiable number of successfully implemented projects at comparable medical device companies in Switzerland or Germany, and always be able to provide prompt support.
The selection process
The demanding specification sheet with basic requirements already meant that the air became thin for many manufacturers of software solutions. The detailed specifications for the individual software modules, the desired module mix and the high expectations regarding the integration of third-party systems, such as the ERP-system and the MES from ARBURG, meant that only CAQ with its modular CAQ.Net software solution remained a suitable supplier.
The implementation of CAQ.Net began immediately in August 2015, with quality assurance solutions for gauge management, initial sample inspection, complaint management and preventive maintenance. The solutions for document management and training management, as well as the web solutions and the audit trail were also added. The final solution was necessary for compliance with the requirements of ISO 13485 and FDA, as it ensures data integrity and aspects of records management.
Central quality control
With the introduction of the module for inspection planning, quality inspection, SPC and LIMS in 2018, CAQ.Net was expanded to a true quality centre at Wild & Kupfer. Thanks to its integrated CAQ-system, the company now has a powerful, multilingual software solution at its disposal, the main advantages of which, according to Daniel Soldini, head of quality management at Wild & Kupfer, are:
- all modules are fully networked and configurable
- third-party systems (ERP) are integrated
- seamless change control and traceability is facilitated
- external access via web applications is possible
- automatic notifications in case of deviations are sent
- ARBURG-ALS data can be statistically evaluated
- all measuring hardware is directly connected
- list evaluations are created and sent automatically
- a very high degree of automation is possible
- the requirements of ISO 9001, ISO 13485, 21 CFR 820 and part 11 are met.
- Compliance and traceability
The future viability of the system was also a key decision factor in the selection of the system. In addition to regular adaptations to technical developments regarding IT-infrastructure, CAQ also ensures that relevant changes to standards, particularly in the area of medical devices, are promptly implemented in the software. Using CAQ.Net software currently allows Wild & Kupfer to always conduct cutting-edge quality assurance with a system that safeguards consistent compliance and traceability, and is ready to meet all challenges that lie ahead.