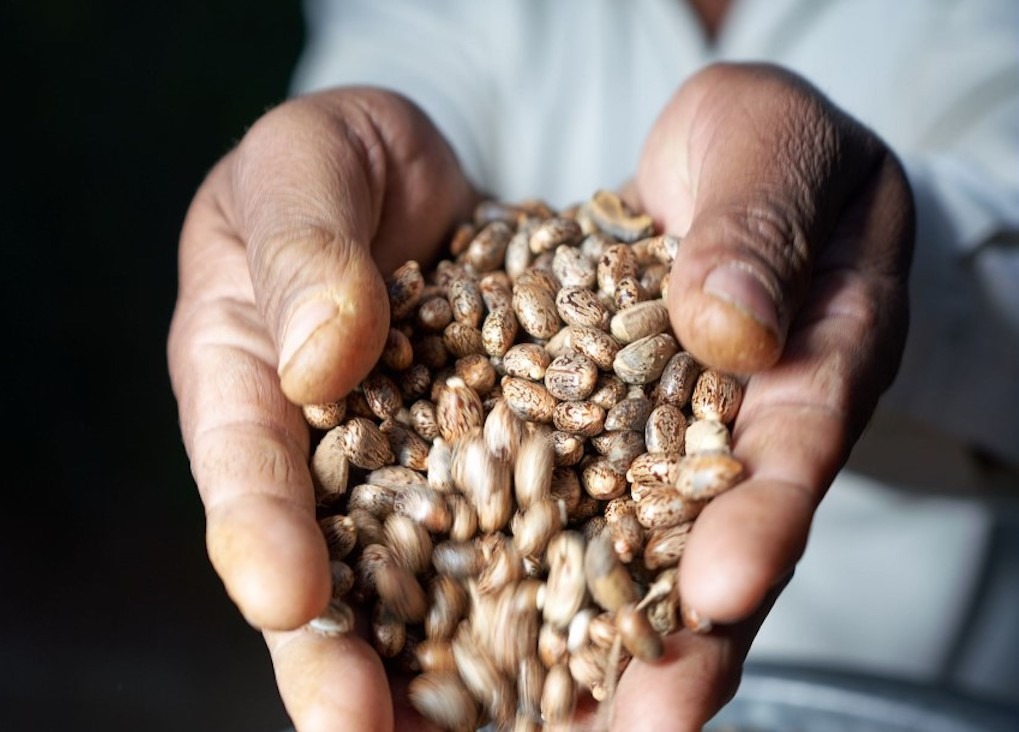
Sustainability continues to be a concern in the world of medical devices, many of which are single use and due to the risk of contamination, not easily recyclable. Arkema health and beauty global market manager Francois Ruas explains how the advanced materials firm has developed its own bio-circular line of medical-grade products and how it recycles them for use in other industries.
When we get to the office we reach for the coffee beans, and for those whose digestive systems punish them for consuming dairy products, we might rely on milk made from soybeans to dilute the bitter taste.
One of the last things we might imagine a bean being capable of is becoming a medical device – but it’s exactly what specialty chemicals and advanced materials French company Arkema is using to create some of their flagship materials
The bean in question is the castor bean, which is actually a seed, but that botanical difference takes nothing away from the impressive transmogrification.
What’s more, the plastic products made from the seed are 100% recyclable and growing more of them hasn’t proven to be an environmental risk.
“It does not compete with feed because it’s growing in the poorest soil in India,” explains Arkema health and beauty market manager Francois Ruas.
“There’s no deforestation, because there’s limited forest where we’re growing them, and the farms have been there for decades, and cultivation is very profitable for the farmers, because they can stock them and sell them on the open trade market.
This is a big difference to other bio-based plastics, as those known as “first generation feedstocks” require the same agricultural conditions as food, meaning expanded cultivation creates competition for land and water use.
What’s more, these first-generation bioplastics make up the bulk of non-petrochemical production and are mostly commodities, meaning the need for a truly advanced sustainable alternative is strong.
How do you get medical-grade plastic from a seed?
Castor beans are crushed to produce castor oil, and it’s this castor oil that undergoes the transformation into a plastic.
“From the oil we make amino 11, which is the monomer that we polymerise down into polyamide 11,” explains Ruas.
The steps taken to create amino 11 and polyamide 11 are, of course, proprietary to Arkema, but the process does involve cleaving the 18 carbon castor oil chain into an 11 carbon (C11) and a 7 carbon (C7) fraction.
The C11 fraction is further reacted in a complex series of highly specific steps to produce the amino 11 monomer, which is then polymerised either alone or in combination with other comonomers to produce polyamide resins.
The beauty of this process is that the C7 fraction has high value as well and is widely used in the personal care industry and the castor cake, left over after the beans crushing step, is highly valued as an effective fertiliser. Nothing is lost!
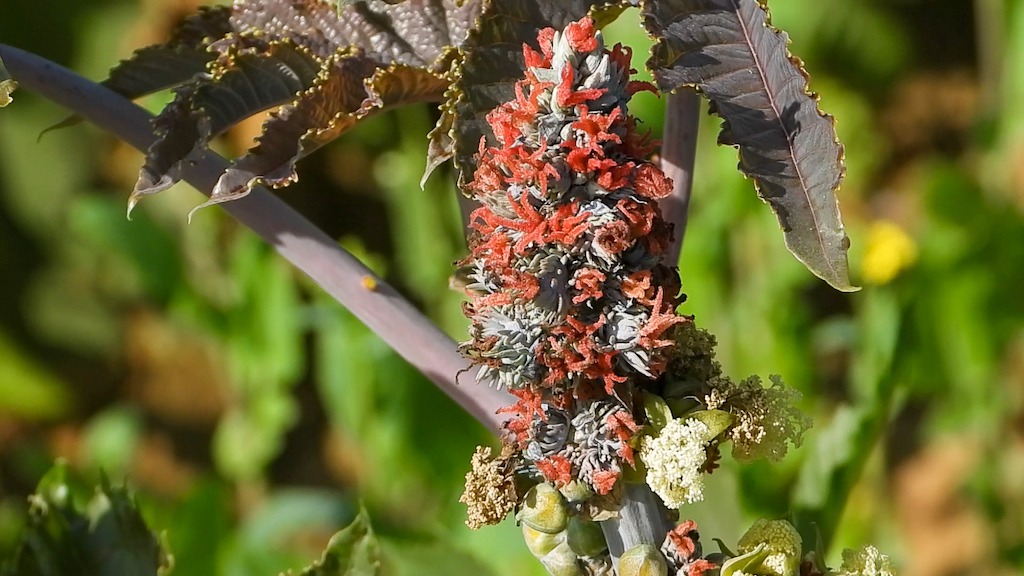
What are the medical uses of polyamide 11?
The actual discovery of polyamide 11 was made in 1947, when the Second World War had exerted a strong demand on the market for raw materials, leading companies using them to search for alternatives.
Initially created by a French company called Organico and sold under the brand name Rilsan, a complex timeline of mergers and acquisitions led to Arkema holding the patents and being the sole producer of Polyamide 11.
As an advanced materials manufacturer, Arkema produces polymers for others to use in their manufacturing process, and the medical device sector is one of many that put the resin through extruders, injection moulders and 3D printers to create their own products.
For the medical device sector, Rilsan polyamide 11 is used to make tubing, balloon catheters and IV bags among others, with a specialist transparent version designed to make any equipment whereby light permeability is important like masks, fittings and connectors.
“Our Rilsan polyamide 11 grades have a common set of properties: they are easy to process, lightweight, chemically resistant, dimensionally stable and tough with good abrasion resistance, which is why we call them advanced polymers.
A plastic and glass hybrid to replace surgical steel and non-sustainable polymers
Ruas, though, is particularly excited about the coming launch of a new Rilsan product.
“It’s a polyamide 11 filled with 65% glass fibres and is designed to replace metal or traditional non sustainable polymers to make single-use surgical instruments,” he says.
“It’s 98% bio based because it’s a mix of glass and polyamide 11 and it is fully recyclable.”
This, he adds, turns a single-use product, which inherently carries its own sustainability challenges, into a bio based one that you can recycle at the end of life – a development he refers to as a “game changer”.
In order to enhance its own offer in this area, Arkema acquired polymer regeneration specialist Agiplast in June this year, giving it the ability to reuse the Rilsan polymers used by its medical customers in the medical industry or in other industries.
According to Ruas, the business now intends to leverage this ability to play matchmaker between companies who have the desire to recycle their final products with those looking to use recycled materials.
What’s next for Polyamide 11?
Of course, as one of the largest chemical manufacturers in the world, not all of Arkema’s products are made from 100% bio based and recyclable materials like Rilsan – but the firm does rank highly on both the Wall Street Journal (#1) and the Dow Jones (#6) sustainability indexes for chemical companies.
What’s more, it has pumped €450m into increasing its manufacturing capabilities in Asia, a move that includes creating the biggest bio-factory producing advanced materials in the world, with the build starting in 2022.
Arkema expects the measures to increase the global capacity of advanced bio-circular polyamide 11 by 50%.