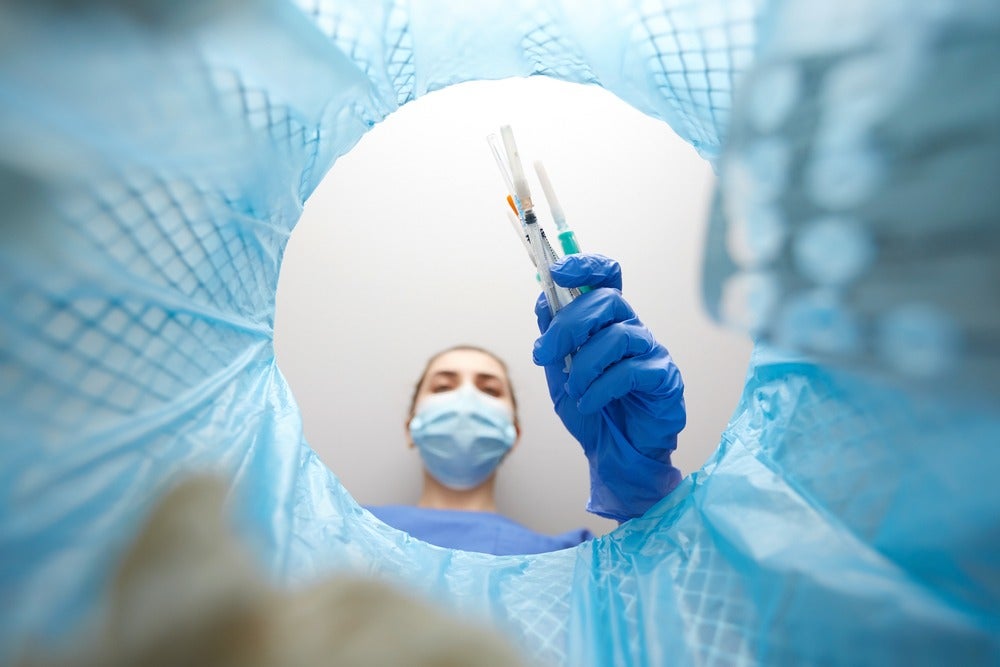
Sustainability is always high up on the agenda when it comes to medical device webinars and conferences, but personal drug delivery devices tend to get a pass because they’re generally not used once and thrown away. Matt Garwood, Principal Engineer at Cambridge Consultants, explains why this needs to change.
We all agree it’s the moral thing to do, right? The world needs to become more sustainable.
We can’t keep throwing away more and more each year without seriously questioning the reasons why.
But surely some products are ok, those that directly improve our health, our wellbeing, our life…surely, they don’t count, do they? Well, I think they do.
Obviously, in an ideal world, everything we use would originate from sustainable sources.
A circular supply chain, where we reuse, repurpose and recycle what we throw away, could see to that.
The trouble with medical devices is that they are designed and manufactured under tight control, to foremost ensure safety and that a reliable product is placed on the market.
However, these all present numerous barriers to reducing environmental impact. Let us look deeper into those barriers in a moment, but I want to be clear from the start.
With a bold, comprehensive response that begins at the concept stage and ends with the user of the device, it is possible to challenge conventional thinking and change for the better.
So, what is it we need to overcome? Within a highly regulated industry, medical drug delivery devices have to provide a safe and efficient means of providing the user with their prescribed medicine.
They must be robust and operate as intended throughout their whole life and they need to provide simple, intuitive interfaces to enable users to use them with minimal training.
Material choices are limited to approved ‘medical grade’ options that have been rigorously tested for suitability to things like biocompatibility with the drug contacting surfaces or patient, sterility, and zero chemical leaching.
In these instances, a recycled route is not an option. A reduced list becomes the first and only choice for designers.
Equally, these medical devices need to fulfil all these requirements at minimum cost, in price-sensitive markets.
Pushing beyond the boundaries
Despite the barriers, the sustainability of drug delivery devices can and should be improved.
The answer is to challenge design decisions throughout the development process – through design, through architectural decisions, through material choice.
By pushing the boundaries of development, innovative materials, and technology, we should also be challenging the business models that place these devices into the market and challenge users to rethink how they interact with their device, so it is not simply thrown away.
Product developers should be considering environmental impact at all stages of device development.
In this way, sustainability sits alongside other criteria to drive innovation, like optimising size, weight, functionality, driving energy-efficient manufacturing methods, pushing forward part design and maximising device life.
Talking about sustainability raises awareness, and development processes incorporating tools like Life Cycle Analysis (LCA) enable engineers to compare designs and material choices and make informed decisions early in the development journey.
Ultimately, this benefits the device design and cost of goods (COGS).
The same goes for the materials we select in our design. Although material choices for drug contacting parts are limited, we could look for new biomaterials for non-critical components like outer caseworks to maximise the life of each device to get as much use out of each as possible.
We should also look beyond the device, carefully considering the end-to-end consequences of design decisions.
These include mapping out the environmental costs across the whole product, packaging, how we display user information in the IFU’s, end of life strategies for disassembling the product into a form that results in the least overall impact, reusing if possible, recycling what you can and using low impact materials for those that must be incinerated.
Engineers and business leaders should challenge the methodology we live by and force innovation to find ways to get the results we need, whilst reducing the impact on the planet.
Most designs are already doing this to minimise cost, optimise manufacture and comply with RoHS (Restrictions of Hazardous Substances) and WEEE (Waste Electrical and Electronic Equipment) directives.
But incorporating sustainability criteria at all levels of the development process will reduce the environmental impact of a design while optimising the design in all other ways.
Helping users change their behaviour
Longer-term, design can help users adapt their behaviour, which might include not throwing away the whole device or providing a recycling route for it.
It may be possible to rethink the business model for drug delivery devices, turning it from a single sale to a returnable approach.
Could devices like preventer inhalers become re-loadable, replenished by the user or manufacturer, with old parts designed for maximum life or washed and recycled at end of life?
Designs could become modular units that can be cleaned, sterilised and reused.
For low-use devices like reliever inhalers, designs could become minimal, with as little waste as necessary.
We should strive for investment into medical grade materials from sustainable sources – be it recycled, bio or other means – to ensure a supply chain with minimal environmental impact.
Ideally, that should be a circular chain, which produces, uses, and returns now and into the future.
In my view, the journey to a sustainable future starts here.