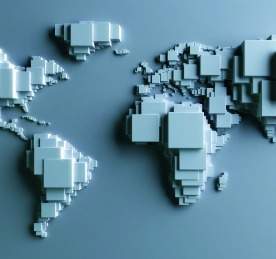
Medical device technology and functionality continues to advance apace, but one area that perhaps doesn’t get as much attention as it should within the design process is materials selection. For many device manufacturers, innovation and R&D within materials is not seen as a core competence and therefore is not lavished with a bespoke in-house materials team, compared with, say, research or investment in the therapeutic, functional or engineering components of a device.
Yet, given the significant R&D investment required to bring a device to market, selecting the right material for use in a new medical device is one of the most critical decisions a manufacturer will need to make. The material, after all, will be a central component in the function of a device, its constraints and limitations. There may also be issues around biocompatibility, regulation and, of course, the cost of the material.
Two of the key obstacles to materials innovation among device manufacturers have been, very simply, cost and risk, concedes Professor Ian Ward, emeritus professor of physics at the University of Leeds.
"One of the problems companies can face is the threat of litigation; that is quite a serious issue," he says. "This has meant there has been a reluctance to go into new materials, for very good reasons. There is bound to be a risk-averse mentality.
"There is less reluctance to go into new processes, but often manufacturers will simply use materials that already have FDA approval. There has to be a requirement to invest considerable resources in all sorts of trials, first on animals and then in vivo and then on people. It has to be gone about very slowly and carefully. There will also need to be serious involvement from many parties, including surgeons and people in medical faculties.
"The safety of the material has to be a big question, of course," he continues. "If it is going to abrade, then whatever abrades has to be absorbed. You can use a bio-absorbable material and, if you can find the right material, you can really improve the wear – something that is a critical issue."
New materials developments
Dental implants is one area where there has been considerable materials innovation in recent years, including the development of orthopaedic/dental implants with hydroxyapatite-bisphosphonate coatings to reduce bone loss more effectively. We are also seeing the increased use of self-reinforced bio-absorbable polymers within the orthopaedic and dental implant arena.
Polymers have, of course, been used within healthcare for decades but, particularly in areas such as orthopaedic or surgical instrumentation, the use of thermoplastic materials and plastic resins is attracting considerable interest. Another area is ‘bioresorbable’ polymers. Although these, again, have been available for more than 40 years, scientists are now focusing on how they can be used in areas such as coatings for drug-eluting stents in order to reduce inflammation and promote more natural healing.
Professor Ward cites work taking place around ‘shape memory’ materials. These are alloys that ‘remember’ their original, cold-forged shape, returning to a pre-deformed shape when heated. Within medicine, such alloys are being used as fixation devices within orthopaedic surgery, particularly for osteotomies, and in braces within dentistry.
Another issue for device manufacturers to consider is the multidisciplinary nature of this type of cutting-edge activity. There will often be common ground between, say, aerospace and engineering when it comes to materials innovation, and therefore collaboration, data and knowledge-sharing can help to eliminate duplication and cost. Working with other sectors can also potentially help device companies think more ‘outside the box’ in terms of materials innovation.
The challenge, as ever, is time and cost, especially given the fact that the selection and use of materials is such a fundamental element of any device, and going down a new avenue, therefore, is a significant undertaking and commitment.
"Materials innovation is a big undertaking," says Professor Ward. "If you are going to redesign a hip prosthesis, say, that is a really big target. The Charnley hip replacement, for example, has not been dramatically improved for more than 30 years, which I think shows the difficulty of these things."