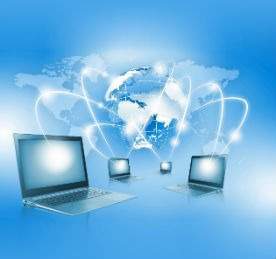
The global drug counterfeiting trade is growing every day. WHO estimates that 7-15% of all medicines in circulation in the developed world are fake, and the figure rises to up to 25% in developing countries. But how do these kinds of drugs make it into the supply chain in the first place? The answer lies in poor serialisation and supply chain management, as well as the complex regulatory environment that governs how pharmaceutical products travel across borders.
The European Union (EU) response to the escalating problem has been obligatory pack serialisation, the standardising of how medical products are labelled and inspected. The result is the Falsified Medicines Directive (FMD), and it comes into force for most EU countries in 2017 – a deadline that’s fast approaching.
There’s a lot for manufacturers to do before they can be fully compliant with the new rules, and the FMD will affect everything from the look and feel of packaging to the ways that production is managed and supply chains are run. The legislation is firmly focused on serialisation and verification requirements, with producers obliged to provide a central EU office with information on all their products, which is passed on to national partners. Clinicians can then verify the barcodes against centralised information to guarantee authenticity.
Manufacturers in the US face similar hurdles. The 2013 Drug Supply Chain Security Act (DSCSA), implemented in three phases over the next ten years, places a major degree of importance on traceability along the supply chain, obligating manufacturers to supply a ‘transaction history’ of all goods. For large manufacturers with big profits, this is not a huge issue, although it is costly; for smaller companies with smaller profits, however, it could be a matter of financial life and death to get compliant by the deadline.
For many such companies, the solution is a simple one: work with a third-party logistics (3PL) provider.
Primed and ready
Many smaller manufacturers outsource their 3PL requirements, often because they don’t usually have the scale to develop a team fully in house, or they need someone else to manage the myriad infrastructure and processes needed to ship directly to customers in other markets.
Amid the clamour to meet the new anti-falsification requirements, one company may have an approach that could be helpful to the industry: Massachusetts-based COVECTRA has launched a serialisation platform aimed at smaller pharmaceutical companies that need to comply with EU and US requirements on medical device traceability in a short space of time.
The platform is called AT Prime, and it uses the company’s AuthentiTrack software to send serialised information to print and packaging facilities, making sure that all goods are compliant with EU – and US, if needs be – regulations. It is an out-of-the-box approach that uses the AT Cloud interface to enable market authorisation holders to send information directly to EU serialisation hubs. According to Steve Wood, COVECTRA president, speaking ahead of the launch, the new system "is cost-effective, powerful, compact and yet provides comprehensive functionality".
"Increasing international regulations such as UDI [Unique Device Identification], FSMA [Food Safety and Modernization Act] and DSCSA are impacting the way companies do business today," he said. "Many manufacturers are struggling to meet compliance in a timely fashion to avoid fines and disruptions to their supply chain network.
"AT Prime was developed to adapt to evolving serialisation-compliance roll-outs, offering a practical, low-cost solution that increases visibility and control, and can be deployed quickly and efficiently to serialise the units of trade to enable track and trace, and deter counterfeiting."
The packaging security technology is applied as additional layers of brand protection, from labels and cartons with proprietary taggants to sophisticated, unique holograms. By combining these layers of security, so the argument goes, a product travels from manufacturing, through packaging to distribution, retail and into the hands of the consumer with maximum traceability, safety and integrity.
"AT Prime is designed for rapid installation and validation, recognising the pressure on today’s pharmaceutical serialisation budgets," Wood told SecuringIndustry.com, a website focusing on anti-counterfeiting.
It works fairly simply: AT Prime provides access to COVECTRA’s AuthentiTrack cloud for direct download to a server. That provides serialised data to the packaging line and to a printer for the primary package.
In many ways, these new regulatory challenges are great for businesses devoted to outsourcing these kind of logistical challenges. Investment and corporate advisory firm N+1Singer, for example, has said that packaging firms are well placed to benefit from new rules in the US.
"Serialisation is expected to increase capex requirements to upgrade legacy packaging lines and bring them into compliance with the new regime," a company statement explains. "In our view, this is likely to drive further outsourcing from pharma companies that are either unable or unwilling to invest."
Choice cut
How does working with 3PL providers on logistics compare with going it alone and will companies that adopt the kind of approach offered by COVECTRA get a better deal? The company’s certainly not the only one in the market offering the kind of platform small manufacturers need to quickly comply with new regulations. California-based med-tech firm rfXcel, for example, recently announced the latest edition of its compliance and serialisation platform designed to massively improve the scope of the existing barcode-scanning technology and functionality.
"The latest product release dramatically improves scalability to handle hundreds of millions of serial numbers, and expands the breadth of global compliance solutions to include China and South Korea," the company announced in a press release.
"The platform enhancements further build on industry-leading serialisation and traceability capabilities, and provide numerous benefits, enabling customers to take advantage of dramatic scale, security and functionality improvements."
Produmex is another software and med-tech company providing outsourced serialisation solutions to medical device manufacturers. Launched, again, as a response to increasingly strict measures by governments and supranational organisations cracking down on counterfeiting, the PDMX Suite expands on the company’s other business software to make serialised item management integral.
"The result is great visibility of inventory by serial number or by batch, combined with on-demand traceability to meet regulatory requirements, for recalls, service and support, and to prevent counterfeiting," Produmex claims on its website, where PDMX Suite is positioned as part of a broader portfolio of products intended to help smaller companies with logistical challenges, from shelf-life management to 3PL services invoicing.
Needs must
While the medical device and pharmaceutical businesses are relatively new to this need to outsource traceability, there are plenty of lessons they can take from another field where end-to-end visibility is critical to staying compliant: the food industry.
Much of the advice given to manufacturers working to keep up with FDA requirements apply equally in these fields, and using 3PL is commonplace in the food sector. For one thing, collaborating with suppliers is essential, and the same traceability challenges exist.
It is certainly tempting for smaller companies and, in some instances at least, outsourcing to 3PL partners means that the regulations can apply differently. In the US, for example, the strict provisions of the DSCSA are not implemented in the same way.
"3PL providers are exempt from these traceability and serialisation requirements," writes Sarah K Rathke, a lawyer specialising in manufacturing litigation at Squire Patton Boggs, "because 3PL handling does not transfer ownership of pharmaceutical products, although we would not be surprised if 3PL customer contracts require 3PLs to collect and maintain this type of information."
"The DSCSA contains interesting new requirements for 3PLs as a result of the federal government’s attempts to create national 3PL pharmaceutical licensing standards. This means that, soon, there will be new 3PL licensing requirements that likely will affect the entire industry. For instance, under the DSCSA, states can no longer regulate 3PLs in the pharmaceutical industry as ‘wholesalers’."
Ultimately, the decision of whether to outsource logistical processes is really dependent on the type of company and its requirements. While it is a necessity for smaller companies, which simply have to outsource, larger manufacturers may also feel compelled to do so to cut costs.
As Neil DeHenes of Cardinal Health Specialty Solutions puts it: "Consider whether it’s in your best long-term financial interest to commit to the continual infrastructure and technology investments needed to comply with constantly evolving state and federal product integrity, track and trace, and support pedigree requirements."
The medical device supply chain industry is big business, recently valued at over $300 billion a year globally, and as regulators crack down on counterfeiting and require increasingly stringent production surveillance, the demands on manufacturers can only grow. In this climate, it’s obvious that turning to 3PL makes sense, but whether it makes money depends on the company.