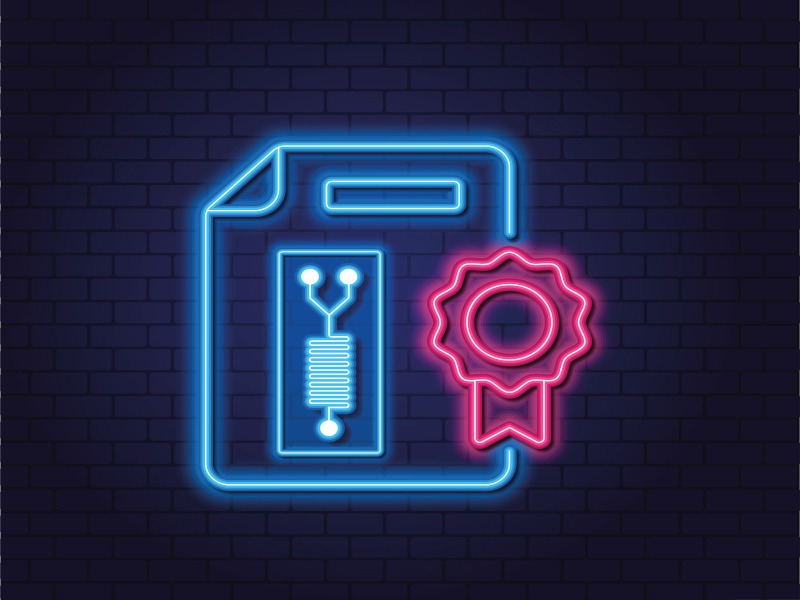
In recent years, there have been extensive discussions between market players that have resulted in cooperation in developing material and technology agnostic standards. This has resulted in the first ISO standard on microfluidic connections and a microfluidic vocabulary. Led by the Microfluidics Association, more than 20 companies from Europe, the US and Japan are now working together to develop a much-wanted standard microfluidic connector.
Another aspect of the microfluidic standardisation endeavour is the standardisation of performance characteristics. As the current testing methods and procedures for microfluidics are generally specific to users, manufacturers or devices, it’s difficult to generalise the results and bring that information back to the design and fabrication stages. The development of industry-wide accepted tests, qualification protocols or generic compliance certificates for microfluidics is therefore seen as key to further improvement. Such tests and protocols should address several key measurement quantities and ensure measurement accuracy and traceability. The challenge is to enable tests that are suitable for a wide range of materials and production schemes. The material and technology independence of the test protocols to be developed will make it possible to include a large number of organisations in the discussions.
Several microfluidic experts were interviewed and, based on their input, a list of the most urgent testing needs was created:
- Pressure decay, flow resistivity and related properties that influence these things, such as wettability, deviation from the ideal dimensions and so on. In particular, the measurement of channel dimensions (in 3D) to determine internal volume and flow restrictions is seen as very important.
- Bonding quality of polymer devices and material properties like glass transition temperature, melting temperature, molecular weight number and distribution.
- Leakage test; burst pressure test; maximum operational pressure test.
- Quality of used materials like optical transmission, auto fluorescence of polymer materials, thickness of glass substrates and so on.
- Calibrated flow measurement tools and methods with an ability to measure fast changing flows.
- Bio viability check after deposition on the chip or in the device.
As seen above, companies that industrialise microfluidic products are in need of protocols for testing the physics behind the performance of devices. Unfortunately, developing and publishing such protocols is seldom a priority for microfluidic scientists and developers. For that reason, a group of scientists, metrologists and industry experts started the EMPIR (European Metrology Programme for Innovation and Research) project MFMET. The goal of this project is to develop the much-needed metrology standards in microfluidics. As a first step, the group defined the operational conditions.
Hot spot in microfluidics
When reading scientific literature, one wonders about the diversity of operational conditions and media used. However, surveys we held indicated that most users are operating their devices at temperatures between 4–50°C or slightly above that and at pressures below two bar. Information from other surveys indicated that the community members are generally working with water-based fluids containing biomolecular matter, and flows between 1μl/min and 100 μl/min.
It was estimated that far more than 75% of microfluidic devices are operating in this hot spot, making it ideal to develop test protocols. The team decided to develop the most urgently needed test protocols first, namely for fast-changing flow rates, leakage measurement and flow resistivity.
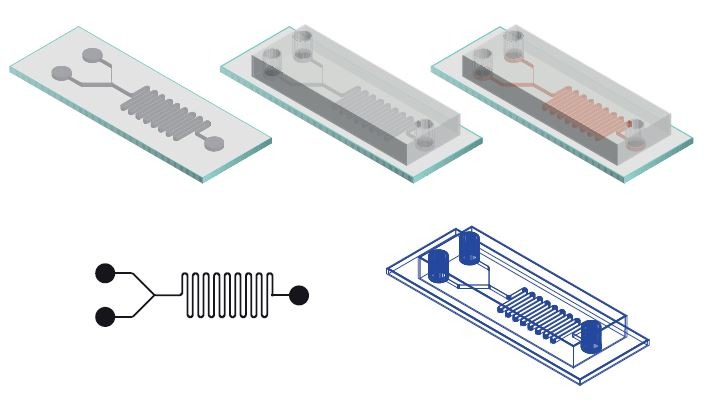
Microfluidic devices are characterised by their speed. During the short time the device operates, accurate control of flow is essential. Diverse types of equipment are used to generate and control flows in microfluidic systems; however volumetric flow rate accuracy has not yet reached a satisfactory level. It is necessary to characterise components within a system to correctly model and predict the system level behaviour and to optimise component usability and interchangeability. Currently, there are no industry-wide accepted tests, qualification protocols or generic compliance certificates to objectively compare microfluidic flow control products from different suppliers.
“Deviation from the intended cross section of microfluidic channels leads to an increase or decrease of the flow resistivity and thereby influencing the performance of the device.”
In a concerted effort to tackle the increasing demand, several national metrology institutes, have already developed protocols and calibration services for micro and nano flow rates. Traceability to national standards has been available since 2012 down to 0.1μl/ min and in 2022 down to 5nl/min, but there is the need to transpose this information to the microfluidic field with its specific demands.
Leakage measurement
Due to the tiny amounts of medium leaking in or out of microfluidic devices, detection is more challenging than leakage in devices with a larger internal volume. To know if a device leaks or not is not enough. Knowledge of the amount of medium leaking from a microfluidic device over a certain period of time is essential for statistical process control, which is needed to safeguard product quality.
After discussion between experts, the first leakage testing protocol was created and published as a whitepaper on the Microfluidics Association website. Due to the diversity of microfluidic devices, there are several protocols applicable. There is a strong preference towards using air or dry nitrogen as a test medium, as it allows the quantitative measurement to be done in a fast and nondestructive way, leaving no contamination inside the microchannels. However, most microfluidic devices use liquids as a work medium, and the relation between leakages of gas and of liquid through small channels is more complex than a difference in viscosity of the media used. Experiments are underway to determine this relation and to develop leakage test protocols that are nondestructive.
Flow resistivity
Deviation from the intended cross section of microfluidic channels leads to an increase or decrease of the flow resistivity and thereby influencing the performance of the device. These deviations can be caused by variations in etching in the case of glass products or deforming during bonding of polymeric products. Surface properties, such as roughness or wettability, will also influence flow resistivity and pressure decay.
The microfluidic industry therefore needs tools and protocols for the measurement of channel dimensions in 3D. The preferred moment for the measurement is for glass-based devices after channel structuring and polymer-based devices after bonding. The ability to measure the entire area of the wafer, or even sample area of it in a short amount of time is desirable and it would give an indication of the process homogeneity and stability over the wafer. It also would predict internal pressure decay and flow resistivity. Particular challenges are the range of sizes to be measured – which can vary from nanometres to hundreds of microns to millimetres – as well the complex cross sections and patterns of devices
Despite the weight of this and other challenges, for the first time in the over 25 years of microfluidic development and industrialisation, serious efforts are ongoing towards the development of standards for this field.